Band saw purchasing advice: how to choose the right product
- What you need to know
- There are two types of electric saws: Table saws and hand saws. Table saws are more powerful, but they are also more expensive and difficult to place.
- A band saw is mainly used for cutting wood. However, there are also models for metal, plastic, textiles, leather and porous concrete, as well as for frozen meat and bones.
- It can make both straight and curved cuts.
- Depending on the saw blade thickness, the saw leaves a rather fine or coarse cut.
- As the cutting height increases, the tension of the band should also increase. Due to the high force exerted, a solid construction of the band saw is a prerequisite.
Precise and uninterrupted sawing
In the world of saws, craftsmen are literally spoilt for choice. Depending on the material and the desired type of cut, it is necessary to use a specific saw. The band saw is a machine that can cut different materials such as wood, plastic, metal, but also leather, textiles or mineral materials as well as bones. In carpentry workshops it is mainly used for cutting curves.
Structure and function of a band saw

A band saw consists of the following main elements:
- Horizontal saw table
- Vertical saw blade
- Idler pulleys
- Band tensioning unit
- Band saw guide and height adjustment
- Motor
The saw blade is a closed ring mounted over two pulleys. These in turn are driven by the motor. Large blocks of wood can be sawn with larger band saws, after which further processing is usually done with a circular saw. The saw table is height-adjustable and, on some models, even adjustable in slope – a clear advantage for anyone who wants to cut mitres and bevels.
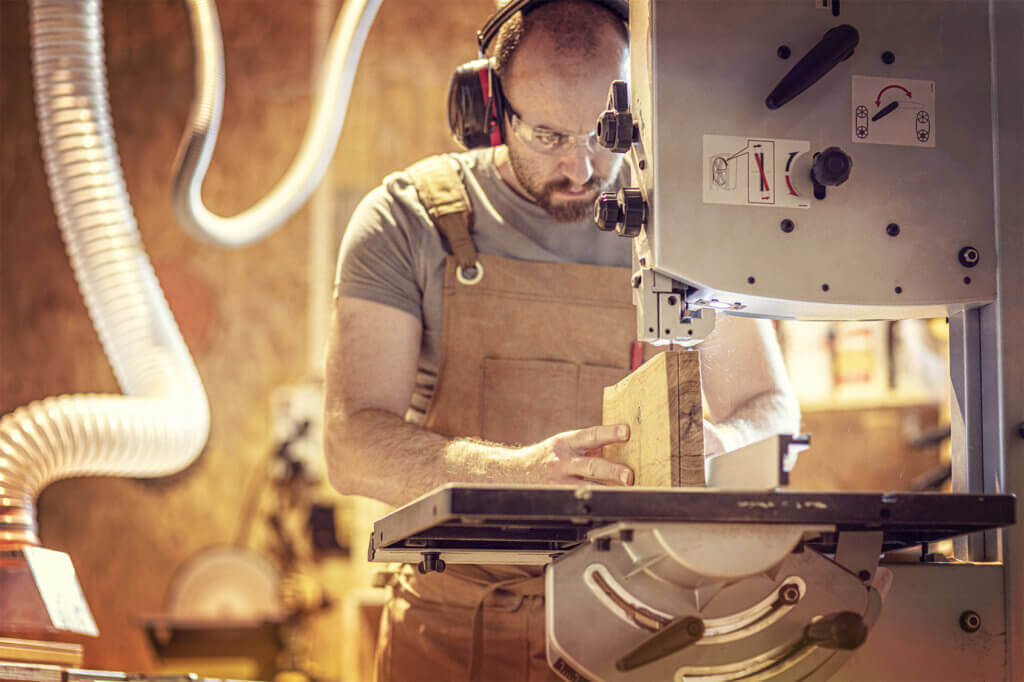
Professionals also prefer the band saw to other machines for cutting soft metals such as aluminium. The band tensioning unit, which has its place centrally behind the upper deflection roller, is responsible for straight cuts in combination with the band guides. The band saw is usually guided by three rollers; two of them are located to the left and right of the saw band respectively and provide lateral guidance. The third roller is mounted behind the saw band and thus prevents the band from retreating when it comes into contact with the workpiece. The possibility of adjusting the height of the band saw guide is used by do-it-yourselfers, among other things, to counteract excessive play of the saw band and consequently an inaccurate cut.
Five reasons to buy a band saw
Besides the band saw, there are numerous other electric saws with similar functions, such as the circular saw or the jigsaw. However, the majority of professional and non-professional craftsmen undoubtedly prefer the band saw when it comes to cutting wood.
We explain why this is so here:
- Cutting strength: unlike normal circular saws, band saws can also cut materials with a thicker diameter without any problems.
- Versatility: Band saws make it easier to cut curvy elements and elaborate designs.
- Quiet working: Unlike circular saws, band saws prove to be rather quiet machines.
- Environmentally friendly: Band saws reduce sawing waste. Since their saw bands are guided very tightly, the cut is much finer.
- Price: Band saws are much cheaper than circular saws.
The different types
The band saw category is further divided into wood band saws, format band saws, metal band saws and cordless band saws:
Wood band saws
In principle, band saws are woodworking machines, although in some cases they can also be used for cutting metal thanks to special bandsaw blades. Often, wood band saws are equipped with an extraction system that allows the material to be processed cleanly, as the sawdust is collected in a specially provided container. In addition, the thin band of the wood band saw enables very fine and precise work to be carried out.
Pro points
- Works quietly and cleanly
- Takes up little space
- Precise cut
Drawbacks
- Mostly fixed parking space required
Sizing band saws
With a sliding carriage, sliding bandsaws are capable of cutting large beams, blocks and insulation material with ease. However, this type of band saw requires more space than the conventional band saw. It is also in a higher price segment.
Pro points
- Very quiet and precise running
- Special saw blade guide
- Precise cutting height adjustment
- Can cut materials of large dimensions
Drawbacks
- Requires a lot of space
- High price
Metal band saws
Equipped with the right band saw blade, a band saw can also be used for cutting metal. Cutting metal causes a lot of friction. Often the saw band overheats as a result. This makes it blunt or unusable and it has to be replaced with a new one. To eliminate this problem, the specialised trade offers metal band saws with special cooling.
Pro points
- Precise finishing of round and corner profiles
- High-quality cut
- Can be used for all metals
Drawbacks
- Difficult to transport
- No internal cuts possible
- High noise level
Cordless band saws
Thanks to its compactness and low weight, the cordless band saw is characterised above all by its flexibility of use. This means that outdoor work or work in places that are difficult to access can also be carried out without any problems. A band saw with battery operation cuts almost all the materials already mentioned. So if you don’t want to be tied to one location, a cordless band saw is the best choice. However, it is advisable to buy a second battery so that work does not come to an unintentional standstill.
Pro points
- Can also be used in hard-to-reach places
- Light and compact
- Flexible
Drawbacks
- Battery must be charged regularly
- Second battery usually costly
- Vibration cannot be ruled out due to light weight
What matters when buying
Whether you are a DIY professional or an amateur – no workshop should be without a band saw. With such a machine, various DIY projects can be tackled in a short time and with little effort.
When it comes to making a final purchase decision, the focus is on knowing how to use the machine and the materials to be processed. The following guide is intended to help all those who are considering a purchase. After all, there are countless band saw models. Before interested buyers decide on a particular model, it is advantageous to know about all the characteristics. Knowing about function and task as well as other important aspects is an important aid to decision-making. The following criteria are also intended to help identify the optimal price-performance ratio:
- Cutting height and cutting width
- Cutting speed
- Idler pulleys
- Table and saw blade guides
- Safety switch and motor brake
- Dimension of saw teeth
- Cutting capacity
- Weight and vibration
- Price
The cutting height and cutting width
The dimensions of a band saw define the working area you have available to process a material. Basic models in the band saw sector can cut wood up to a diameter of 70 to 80 millimetres. Industrial models, on the other hand, can handle diameters of up to 1,200 millimetres. The same values apply to metal band saws. Depending on the thickness of the material that is mainly being worked with, this aspect must be taken into account.
The cutting width corresponds to the effective distance between the saw blade and the next vertical element. Usually this is the fence. Most band saws have a cutting width between 15 and 35 centimetres. On professional machines, the width is much greater.
The cutting speed
The cutting speed (abbreviation: m/s) refers to the number of metres the saw blade passes in one second. When it comes to speed, there are significant differences between the individual models. Basic models achieve cutting speeds of 3 to 15 metres per second. Higher quality band saws allow even higher cutting speeds. This is an ideal option for adapting the saw’s cut to different materials.
In addition, the more expensive models have multi-stage switches. This allows craftsmen to easily increase or decrease the cutting speed, depending on the resistance of the material, and as a result achieve far more precise cuts. To keep resistance as low as possible, we recommend working at the highest possible speed.
The pulleys
Band saws contain two or three guide pulleys whose job is to turn the saw band. On models with two pulleys, they are always one above the other, with the lower one connected to the motor that sets the pulley in motion. This in turn transmits the movement forces to the saw band. On band saw types with only two deflection rollers, the cutting width cannot be greater than the diameter of the deflection rollers.
To be able to cut materials with a larger width, a band saw with three deflection rollers is needed. The disadvantage of this type of saw is the sluggish running of the saw band. In addition, the saw band is damaged more quickly. Here, models that are self-cleaning and thus prevent the accumulation of sawdust within the system are advantageous.
The table and the saw blade guides
Usually the tables are made of sheet metal, wrought iron, steel or aluminium, with the aluminium models being the most balanced. The saw tables are equipped with grooves so that there is no accumulation of sawdust and sawdust on the table. In addition, the tables should be tiltable by 45 degrees to be able to realise bevels and mitres.
At the beginning of the sawing process, the saw band often tends to jump off the deflection rollers. This can be counteracted by using bandages on the band or deflection rollers as well as saw band guides in the form of small rollers to the left and right of the saw band. Often, band saws have a third roller directly behind the saw band, so that the cut can be made accurately and cleanly even if there is a lot of resistance.
The safety switch and the motor brake
For safety reasons, the motor that drives the saw band starts and stops automatically. The band must also stop automatically when the doors to the pulleys are opened. In certain environments, such as schools, the band saw can only be started up with a separate key.
The dimensions of the saw teeth
The number of saw teeth per inch (tpi = teeth per inch) gives the dimension of the teeth. One inch corresponds to 2.54 centimetres. The thicker the material to be sawn, the greater the number of saw teeth needed to cut it. Therefore, in order for wood to be cut cleanly and precisely, it needs a higher tpi value compared to industrially processed woods such as chipboard.
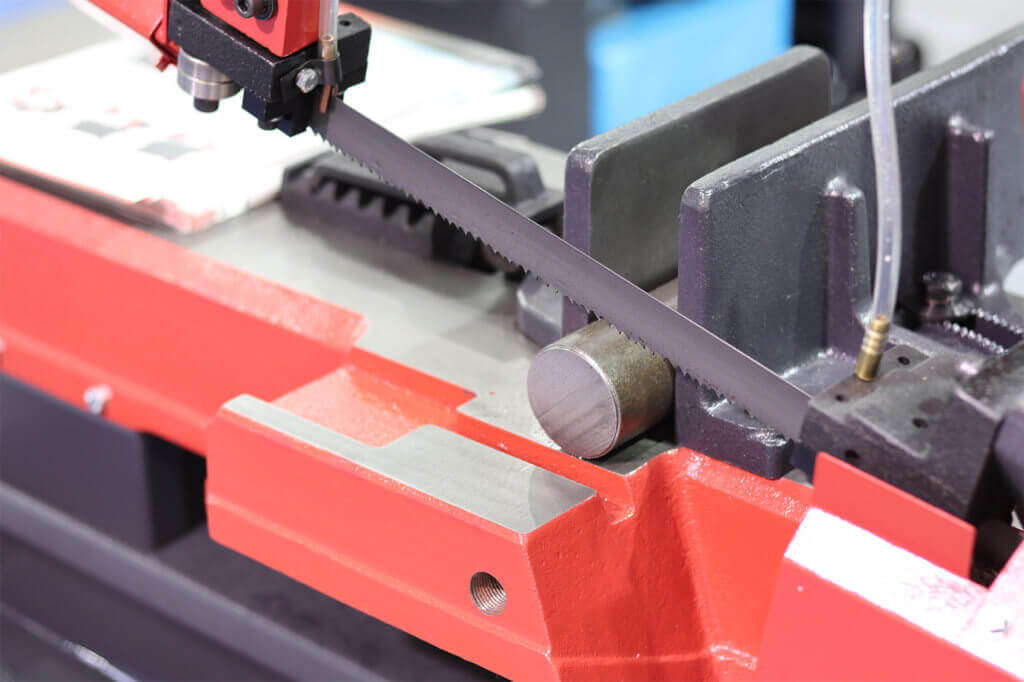
The cutting ability
With a band saw, professionals and do-it-yourselfers can make many different cuts. This makes the electric tool a valuable helper when it comes to material processing. In addition to intricate shapes and curves and complex joints, these machines can also rip boards widthwise. This means that nothing stands in the way of producing veneers at home.
Weight and vibration
A heavy weight guarantees a good stability and thus reduces the vibration of the band saw. As a result, the band saw inevitably produces an accurate and clean cut. Therefore, this aspect should also be considered when making a purchase decision. Most stationary band saws are characterised by an ideal weight.
The price
The prices for band saws vary greatly and depend on the criteria mentioned above as well as their qualitative performance. Basic models start at prices from 150 euros. This sum increases in correlation with factors such as motor power, the presence of an exhaust system or saw blade cooling. Very high-quality models reach prices of several thousand euros. However, such professional machines are not necessary for DIY use.
Tips for care and maintenance
If you want to enjoy a well-functioning band saw for a long time, you need to pay attention to some aspects regarding care, cleaning and maintenance.
Cleaning the inside of the machine and the deflection rollers
Sawing produces sawdust and sawdust that is deposited in and on the saw. For this reason, you should thoroughly vacuum the saw with a workshop vacuum cleaner every day or after use. Avoid using compressed air, as this can do more harm than good. Pay particular attention to the lower machine housing, as this is where most of the dust settles.
Also, every time you change the saw band, check the band linings for deposits or defects and replace them if necessary. The scraper brush, which removes the coarsest dirt from the guide pulley, should also be checked, cleaned and replaced if worn.
Cleaning and lubricating the saw blade guides
We should mention at the outset that there are manufacturers who do not recommend lubricating the saw band guides. Others explicitly recommend lubrication with special oils. Either way, you should first clean the sensitive guides from dirt and dust. Once this work is done, oil and lubricate the rollers according to the manufacturer’s instructions. This guarantees smooth running of the saw blade guides, which also benefits the saw blade as it does not wear out as quickly.
Relaxing the saw band when not in use
To protect the saw band, whose weld seam is very sensitive, and the bandages of the deflection rollers from impressions and subsequent tears, you should always relax the band after you have finished working. To do this, it is also essential to lubricate the thread of the covering from time to time so that it does not snag and can be turned easily. Not all manufacturers point this out.
Checking drive belts and other wearing parts
If the drive belt stretches after initial use of the band saw, this can cause the machine to make a squeaking noise when it is started up. Then it is time to tighten the belt. The belt must not give inwards by more than 5 to 6 millimetres when pressed. If you notice cracks in the drive belt, you must replace it immediately. This also applies to all other wearing parts of the band saw. To avoid major damage, it is advisable to check and replace all spare parts regularly.
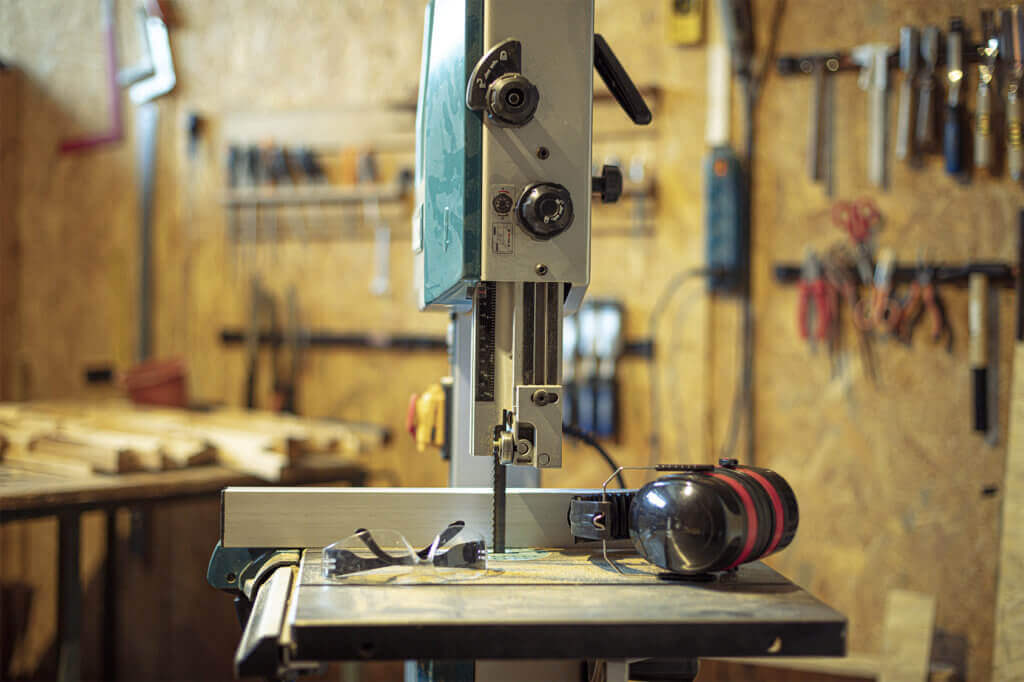
Further tips for correct application
To avoid unwanted slipping of the material, it is important to make sure that the base is stable before working. In addition to the saw, the workpiece must also be cleaned regularly. If the workpiece is dirty, the dirt is transferred to the saw blade, which in turn starts to hook and causes an imprecise cut.
There is a suitable saw blade for every type of cut, whether for precise and straight cuts or for contour cuts. The all-rounder among the saw blades is probably the flexback bandsaw blade. This standard variant is not only distinguished by its wide range of applications, both for wood and for all non-ferrous metals. It is also one of the cheaper saw blades.
In contrast, there are the hardback band saw blades. These are specialists with a spring-hard back and specially hardened saw teeth. This combination enables extremely precise cuts. Another advantage is the high tensile strength. However, this is also reflected in a higher price. For sawing gas and aerated concrete as well as Ytong, saw blades with carbide-tipped teeth are offered, which facilitate the cutting of the mineral materials and lead to less wear of the saw blades. Band saw blades with tungsten carbide tips are used for cutting vehicle tyres, brake linings, fibreglass and composite materials.